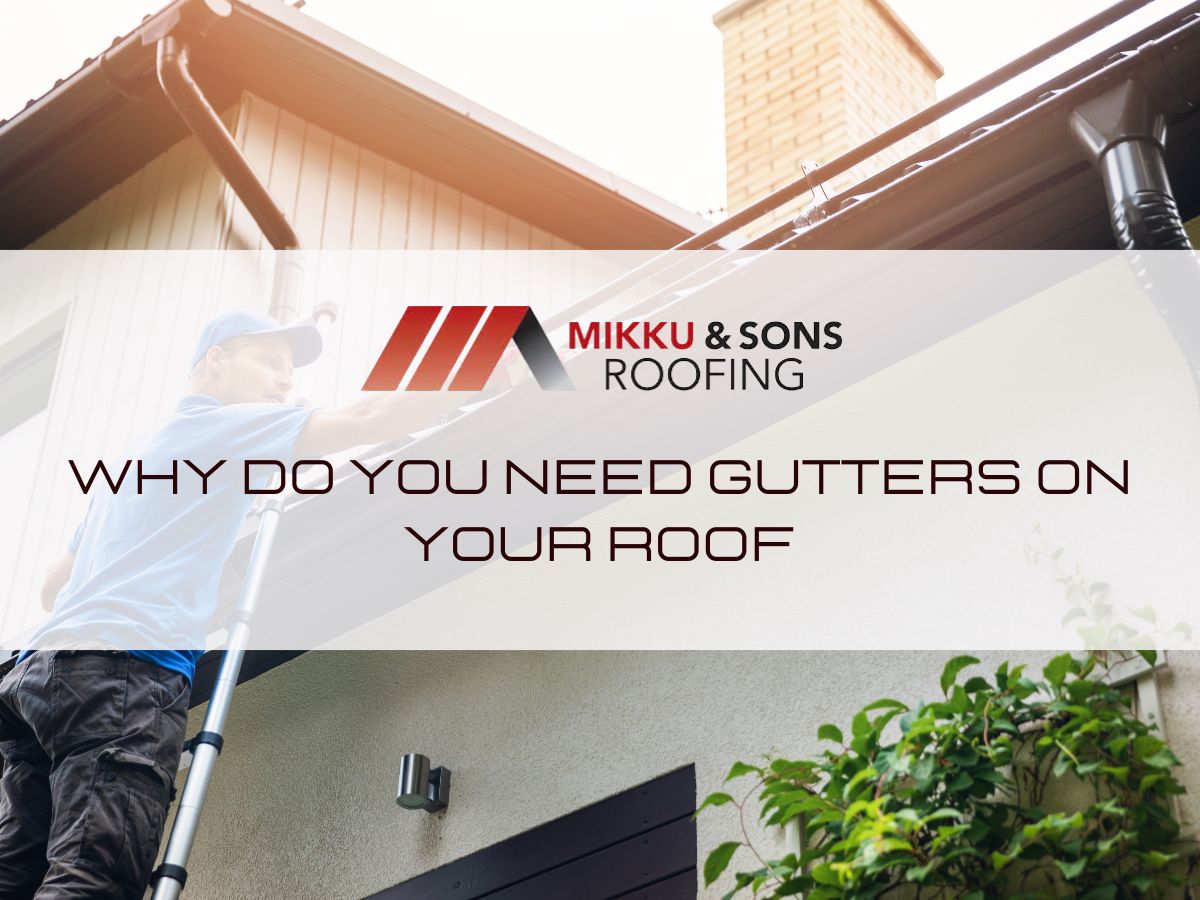
With so many advantages over conventional roofing materials, including durability and energy efficiency, rubber roofing has become a popular substitute. The focus has shifted to rubber roofing as a feasible choice for residential, commercial, and industrial applications alike in the search for affordable and ecological building solutions.
Rubber roofing is becoming more and more cost-effective, and this has prompted contractors, company owners, and homeowners to learn more about how important it is to make decisions that balance initial costs with long-term savings. It is important to assess roofing systems' lifecycle costs and environmental impact in addition to their original investment, given the ongoing evolution of the building sector.
Rubber roofing presents a versatile solution suitable for various types of roofs, spanning residential, commercial, and industrial applications. Unlike some traditional roofing materials, rubber roofing can adapt to different roof shapes and sizes, making it an attractive option for a wide range of structures.
Its flexibility and durability make it particularly well-suited for flat and low-slope roofs, where other materials may be prone to leaks or damage.
Rubber roofing has gained popularity among homeowners seeking durable and low-maintenance roofing solutions. It is especially suitable for residential properties with flat or low-slope roofs, such as modern-style homes or those in areas prone to heavy rainfall.
Additionally, rubber roofing's ability to withstand extreme weather conditions makes it an ideal choice for homes located in regions with fluctuating climates.
Commercial buildings often feature flat or low-slope roofs, making rubber roofing a practical choice for these structures. From office complexes to retail outlets, rubber roofing offers commercial property owners a cost-effective and long-lasting solution for protecting their investments.
Its versatility extends to various commercial roof types, including warehouses, shopping malls, and restaurants, where durability and weather resistance are paramount.
Industrial facilities require robust roofing solutions capable of withstanding harsh environments and heavy usage. Rubber roofing meets these demands with its exceptional durability and resistance to chemicals, UV rays, and temperature fluctuations.
Whether it's a manufacturing plant, distribution center, or industrial warehouse, rubber roofing provides reliable protection against leaks and structural damage, ensuring uninterrupted operations and minimizing maintenance costs over time.
Rubber roofing encompasses various types of materials, each offering unique characteristics and cost considerations. Understanding the differences between these options is essential for making informed decisions regarding the most suitable roofing solution for your project.
EPDM (Ethylene Propylene Diene Monomer) roofing is a popular choice for rubber roofing applications due to its exceptional durability, flexibility, and cost-effectiveness. EPDM membranes are made from a synthetic rubber compound that exhibits superior resistance to UV radiation, ozone exposure, and weathering, making them ideal for use in various climates.
EPDM roofing systems are commonly installed on flat or low-slope roofs in residential, commercial, and industrial buildings, providing reliable protection against leaks and structural damage.
EPDM roofing membranes are available in two primary formulations: black EPDM and white EPDM. Black EPDM is the traditional choice, offering excellent heat absorption and thermal stability, while white EPDM provides enhanced reflectivity and energy efficiency.
Both formulations are highly resistant to ozone, UV radiation, and extreme weather conditions, ensuring long-term durability and performance. EPDM roofing membranes typically come in large rolls, ranging from 45 to 60 mils in thickness.
Thicker membranes offer increased puncture resistance and longevity, making them suitable for high-traffic areas or regions prone to hail and debris. EPDM roofing systems can be installed using various methods, including fully adhered, mechanically fastened, or ballasted systems.
Each installation method offers unique advantages and is chosen based on factors such as roof slope, building height, and local building codes.
The cost of EPDM roofing materials varies depending on factors such as membrane thickness, membrane type (black or white), and project size. On average, EPDM roofing materials can cost between $3 to $7 per square foot for residential applications and up to $10 per square foot for commercial or industrial projects.
Installation costs for EPDM roofing depend on factors such as labor rates, roof complexity, and installation method. On average, installation costs range from $5 to $10 per square foot for residential projects and up to $15 per square foot for commercial or industrial applications.
While EPDM roofing may have a higher upfront cost compared to some other roofing materials, its long lifespan of 25 to 30 years and minimal maintenance requirements make it a cost-effective investment in the long run, providing property owners with reliable protection and peace of mind.
TPO (Thermoplastic Polyolefin) roofing has emerged as a popular choice for rubber roofing applications, prized for its exceptional weather resistance, energy efficiency, and ease of installation. TPO membranes are composed of a blend of polypropylene and ethylene-propylene rubber, offering superior flexibility, heat reflection, and UV stability.
TPO roofing membranes are available in a variety of thicknesses, typically ranging from 45 to 80 mils. Thicker membranes offer increased durability and puncture resistance, making them suitable for high-traffic areas or regions prone to severe weather conditions.
TPO membranes are available in different colors, including white, tan, and gray, with white TPO being the most common choice due to its high reflectivity and energy efficiency. White TPO reflects sunlight, reducing heat absorption and lowering cooling costs, making it an environmentally friendly and cost-effective roofing option.
TPO roofing membranes are inherently resistant to UV radiation, ozone exposure, and chemical pollutants, ensuring long-lasting performance and minimal maintenance requirements. Additionally, TPO membranes are recyclable, contributing to sustainability initiatives and environmental responsibility.
The cost of TPO roofing materials varies depending on factors such as membrane thickness, color, and project size. On average, TPO roofing materials can cost between $4 to $8 per square foot for residential applications and up to $10 per square foot for commercial or industrial projects.
Installation costs for TPO roofing depend on factors such as labor rates, roof complexity, and installation method. On average, installation costs range from $6 to $12 per square foot for residential projects and up to $15 per square foot for commercial or industrial applications.
While TPO roofing may have a slightly higher upfront cost compared to some other roofing materials, its superior energy efficiency, durability, and long-term performance make it a cost-effective investment in the long run, providing property owners with reliable protection and significant energy savings.
PVC (Polyvinyl Chloride) roofing represents another popular option for rubber roofing applications, prized for its exceptional durability, chemical resistance, and weatherproofing properties. PVC membranes are composed of reinforced thermoplastic material, offering superior flexibility, heat reflectivity, and resistance to UV radiation.
PVC roofing membranes are available in various thicknesses, typically ranging from 45 to 80 mils. Thicker membranes offer increased durability and puncture resistance, making them suitable for high-traffic areas or regions prone to severe weather conditions.
PVC membranes are inherently resistant to UV radiation, ozone exposure, and chemical pollutants, ensuring long-lasting performance and minimal maintenance requirements. Additionally, PVC roofing membranes feature welded seams, providing superior strength and watertight seals to prevent leaks and water infiltration.
PVC roofing membranes are available in different colors, including white, tan, and gray, with white PVC being the most common choice due to its high reflectivity and energy efficiency. White PVC reflects sunlight, reducing heat absorption and lowering cooling costs, making it an environmentally friendly and cost-effective roofing option.
The cost of PVC roofing materials varies depending on factors such as membrane thickness, color, and project size. On average, PVC roofing materials can cost between $5 to $10 per square foot for residential applications and up to $12 per square foot for commercial or industrial projects.
Installation costs for PVC roofing depend on factors such as labor rates, roof complexity, and installation methods. On average, installation costs range from $7 to $15 per square foot for residential projects and up to $20 per square foot for commercial or industrial applications.
While PVC roofing may have a slightly higher upfront cost compared to some other roofing materials, its superior durability, chemical resistance, and long-term performance make it a cost-effective investment in the long run, providing property owners with reliable protection and significant energy savings.
Assessing the cost-effectiveness of rubber roofing involves considering various factors, including initial installation costs, long-term maintenance expenses, durability, and energy efficiency. Rubber roofing, such as EPDM, TPO, and PVC membranes, offers several advantages over traditional roofing materials like asphalt shingles, metal, and built-up roofing (BUR) systems.
Rubber Roofing (EPDM, TPO, PVC): Rubber roofing typically has moderate to high initial installation costs compared to asphalt shingles but is comparable to or slightly higher than metal roofing. The cost varies based on the type of rubber roofing material, membrane thickness, installation method, and project size.
Asphalt shingles are the most common roofing material for residential properties due to their low initial cost. However, they have a shorter lifespan compared to rubber roofing and may require more frequent repairs or replacements.
Metal roofing has a higher initial cost than rubber roofing but offers excellent durability and longevity. While the upfront investment may be higher, metal roofing can provide long-term cost savings due to its extended lifespan and minimal maintenance requirements.
BUR systems involve multiple layers of roofing felt and asphalt or tar, making them labor-intensive and costly to install. While BUR systems have been widely used in the past, they are less common today due to their high installation and maintenance costs.
Rubber Roofing: Rubber roofing requires minimal maintenance over its lifespan, reducing long-term maintenance costs. Periodic inspections and simple repairs, such as patching or seam resealing, may be necessary but are relatively inexpensive compared to other roofing materials.
Asphalt shingles may require regular maintenance, including replacement of damaged or missing shingles, cleaning of debris, and inspection for signs of wear or deterioration. Over time, the cost of maintenance can add up, particularly in regions with harsh weather conditions.
Metal roofing is low maintenance and resistant to pests, rot, and fire. While metal roofs may require occasional cleaning to remove debris and prevent corrosion, they generally have lower long-term maintenance costs compared to asphalt shingles.
BUR systems require regular inspections and maintenance to prevent leaks, cracks, and moisture infiltration. Maintenance tasks may include patching, resealing seams, and applying protective coatings, resulting in ongoing expenses.
Rubber Roofing: EPDM, TPO, and PVC membranes have a lifespan of 20 to 30 years or more when properly installed and maintained. Rubber roofing is resistant to UV radiation, extreme temperatures, and weathering, ensuring long-term durability and performance.
Asphalt shingles typically have a lifespan of 15 to 25 years, depending on the quality of the materials and installation. Shingles may degrade over time due to exposure to sunlight, moisture, and temperature fluctuations, requiring replacement.
Metal roofing can last 40 to 70 years or more with minimal maintenance. Metal roofs are resistant to fire, pests, and rot and can withstand harsh weather conditions, making them a durable and long-lasting roofing option.
BUR systems have a lifespan of 20 to 30 years but may require more frequent maintenance and repairs compared to other roofing materials. Over time, the layers of asphalt or tar may degrade, leading to leaks and structural issues.
Rubber roofing, including EPDM, TPO, and PVC membranes, offers a compelling combination of durability, low maintenance, and long-term cost-effectiveness for residential, commercial, and industrial applications. While the initial installation costs of rubber roofing may be higher compared to traditional materials like asphalt shingles, metal, or built-up roofing (BUR) systems, the investment pays off over time.
Roof flashing serves as a critical component in maintaining the integrity of the roofing system by sealing joints, transitions, and penetrations to prevent water infiltration. Properly installed flashing directs water away from vulnerable areas, such as chimneys, vents, skylights, and roof edges, minimizing the risk of leaks and water damage.
Incorporating robust flashing systems further enhances the resilience of the roofing system, providing added protection and peace of mind.